CNC machine NESTING KDT KN-3710D
The KDT KN-3710D CNC nesting machine is the most you can get for your money. It is characterized by great processing accuracy, processing speed, productivity, flexible use of milling and drilling, easy upgrade with transport devices and an extremely affordable price. The focus of the KDT nesting machine is on cutting, as it enables fast, high-quality processing with suitable tools even at 25 m/min.
The Italian manufacturer's TPA CAD software is a well-known software tool used by well-known CNC machine manufacturers such as Felder, Brema, Vitap and Busellato.TPA CAD is a parametric program with a powerful 3D graphic interface for the production of flat furniture, it is easy to use and powerful and flexible enough even for more demanding users. The additional CADNESTING module is included in the standard equipment and enables effective optimization of the cutting of workpieces of regular and irregular shapes for maximum material utilization.
More information about the software:
With the additional MPR importer module it is possible to use programs of Homag CNC machines.The machine can be connected to various programs for designing furniture, such as MegaTischler, Corpus 3D, Imos, Sword, Solidworks, Alphacam and LestrojBox.
CNC NESTING KDT KN-3710D machine
KDT KN-3710D is basically made of welded steel industrial construction, which means that the machine is very robust, it has almost zero vibrations even during fast accelerations and movements up to 80 m/min (vector speed 113 m/ min!) and ensures precise processing and high productivity. In addition to the robust construction (weight of the basic machine 4800 kg), all important parts from renowned manufacturers such as HSD, TPA, DELTA, Helubel, Becker, Simpo, PMI and Pneumax contribute to reliable operation. p>
KDT nesting is equipped with an extremely powerful 13.2 kW electric HSD (Biesse Group) engine with HSK-F63 and fast turret 12-position tool magazine and tool length sensor.
- Drilling unit KDT contains nine vertical bits for drills, four along the X axis and five along the Y axis.
- The work table is a matrix with six vacuum zones and two Becker vacuum pumps with a total capacity of 500 m3/h, which enable stable processing of even smaller workpieces.
- The machine already has an automatic material pusher from the machine (significantly increases productivity and eases work) and vacuum grippers for loading and positioning the workpiece.
- Side guides on both sides are already standard equipment, they serve as zero points and as a guide when moving workpieces from the work table to the conveyor belt >.
- This avoids the high costs of later upgrading the machine with automatic loading and unloading.
- The lifting table and the conveyor belt can be added later at no great cost.
- Possibility of upgrading with automatic labeling to the entrance lifting table with ZEBRA printer.
- The machines are manufactured according to EU safety standards and have a valid CE certificate.Protective fence and safety photocells are part of the standard equipment.
- KDT machines are very reliable and have the best price-quality ratio!
Different dimensions of work tables
Three dimensions of the machine work table are available:
- KN3409: 2740 × 1220 mm,
- KN3710: 3060 × 2150 mm,
- KN3130: 4260 × 2150 mm,
- Z axis: 180 mm.
Technical characteristics and equipment of the KDT KN-3710D CNC machine:
- working dimensions: 3060 × 2100 × 200 mm,
- feed speed (X, Y, Z): 75/75/20 m/min,
- PLC controller: TPA (Italy),
- main milling unit HSD (Biesse Group) – HSK – F63 taper – 13.2 kW (17 HP),
- tool blowing,
- drilling unit of nine vertical drills HSD or KDT (6000 rpm), 1.7 kW engine with suction,
- pneumatic shutters for extraction (switch between milling machine/drilling unit/extraction cap for the workbench),
- extraction cap for the table + workpiece pusher - simultaneous loading of the plate on the table and push of the processed pieces from the work table to the conveyor belt,
- turret tool changer 12 positions - quick change,
- zero points with an integrated guide bar for plate alignment and maximum stability of workpieces during pushing from the work table to the conveyor belt,
- sensor for measuring tool length,
- special HELUKABEL cable from a German manufacturer for long-term uninterrupted work,
- TPA Software,
- vacuum pump Becker VTLF.2.250, 250 m3/h - two pieces - total flow 500 m3/h,
- weight of the basic machine: 4800 kg,
- the machine is manufactured according to CE standards (safety fence + photocells).
Advantages and special features of the KDT KN-3710D CNC nesting machine
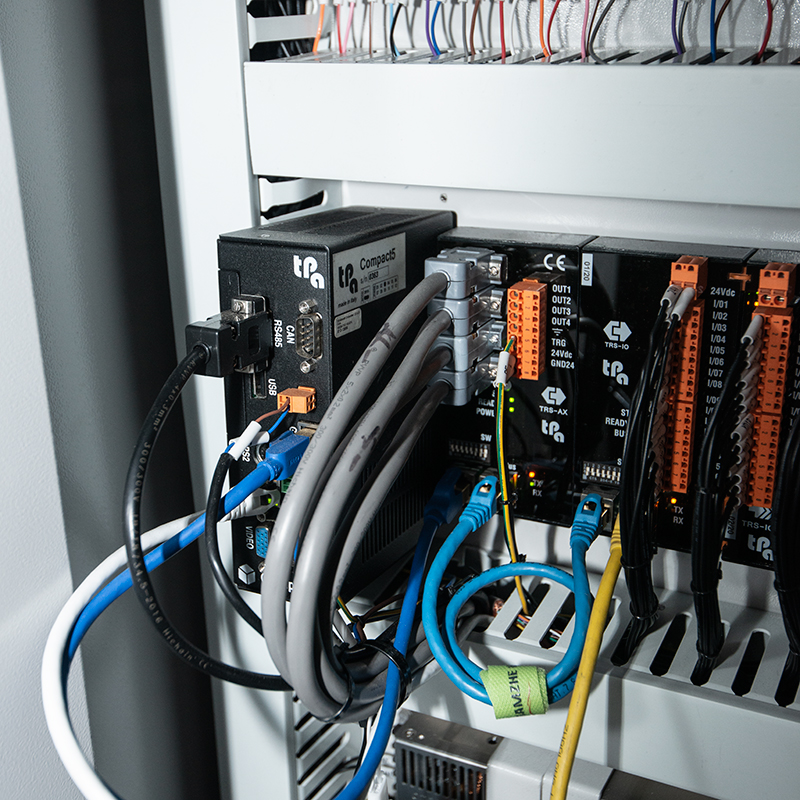
The machine has a powerful, reliable controller from the Italian manufacturer TPA, its own innovative TPA CAD software and an additional module in Slovenian called TPA NESTING on a Lenovo PC. TPA controllers are used by well-known European CNC machine manufacturers such as Busellato, Alberti and Format 4 (Felder).

The machine features a powerful milling unit from the Italian manufacturer HSD (Biesse Group) - 13.2 kW (17 HP), air-cooled, with a Delta frequency converter for stepless adjustment of the milling cutter rotation speed from 3,000 to 24,000 rpm and reliable HSK clamping -F63.
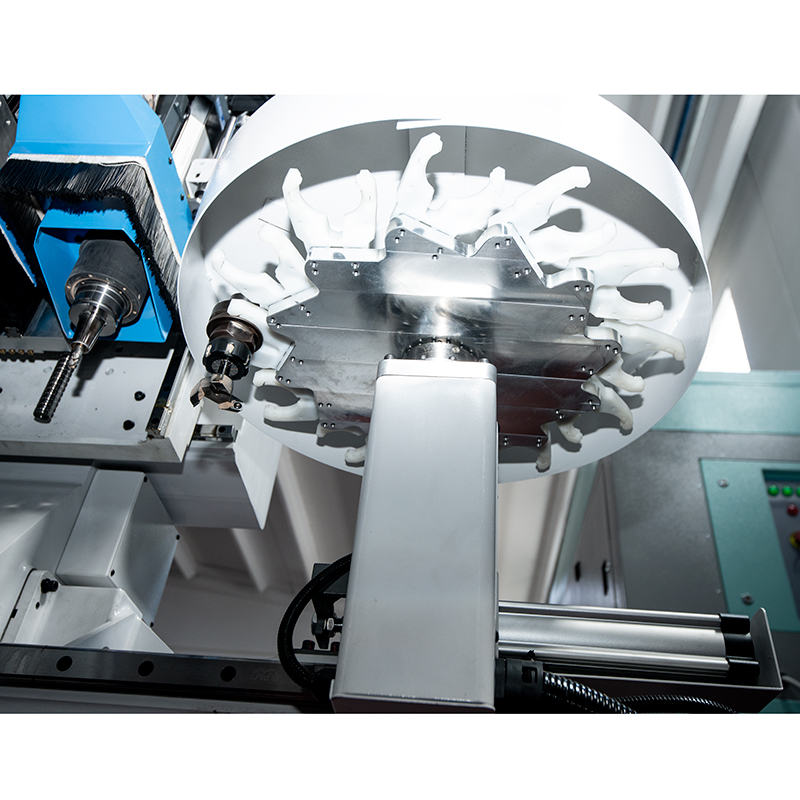
The machine is equipped with a fast revolver magazine with 12 positions, it is driven by a servo motor, which is installed directly on the bridge of the machine and with which it moves together. This means a shorter tool change time and consequently higher productivity.
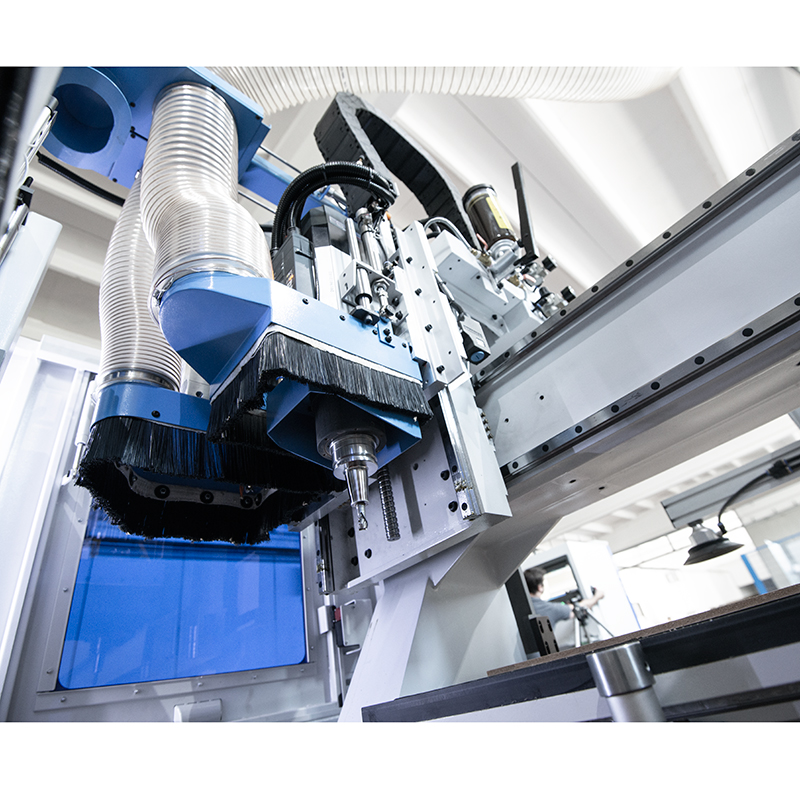
The machine has an independent KDT drilling unit with nine vertical drills (five along the X axis, four along the Y axis). The drilling stroke is 60 mm, each drill bit is independent.
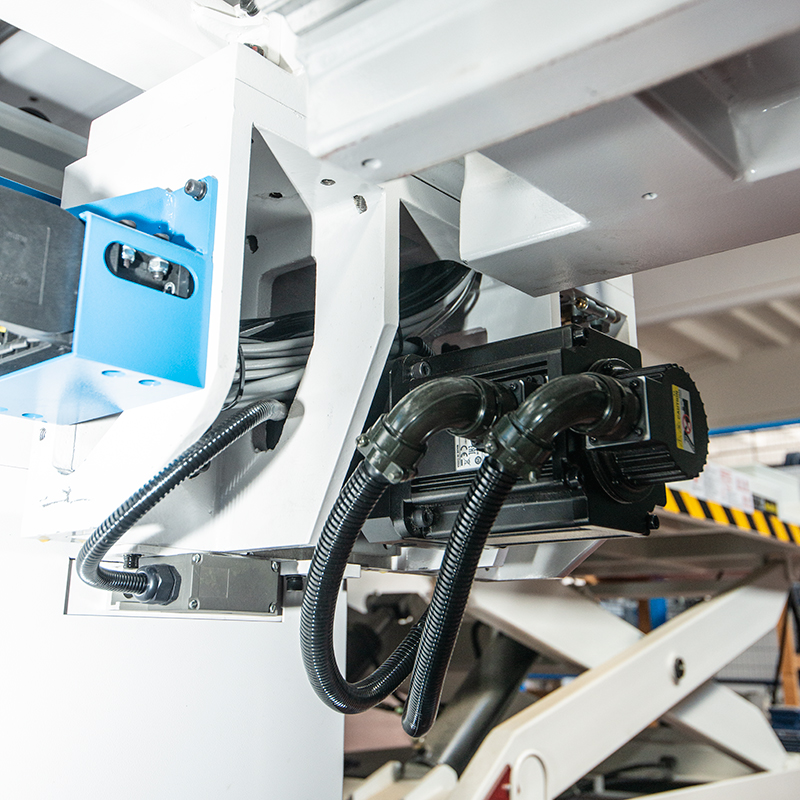
Precise positioning and fast movements with two powerful, mutually electronically SYNCHRONIZED DELTA servo motors with a power of 1300 W for maximum accuracy and accelerations of the Delta frequency converter and the gear of the Japanese manufacturer Simpo.
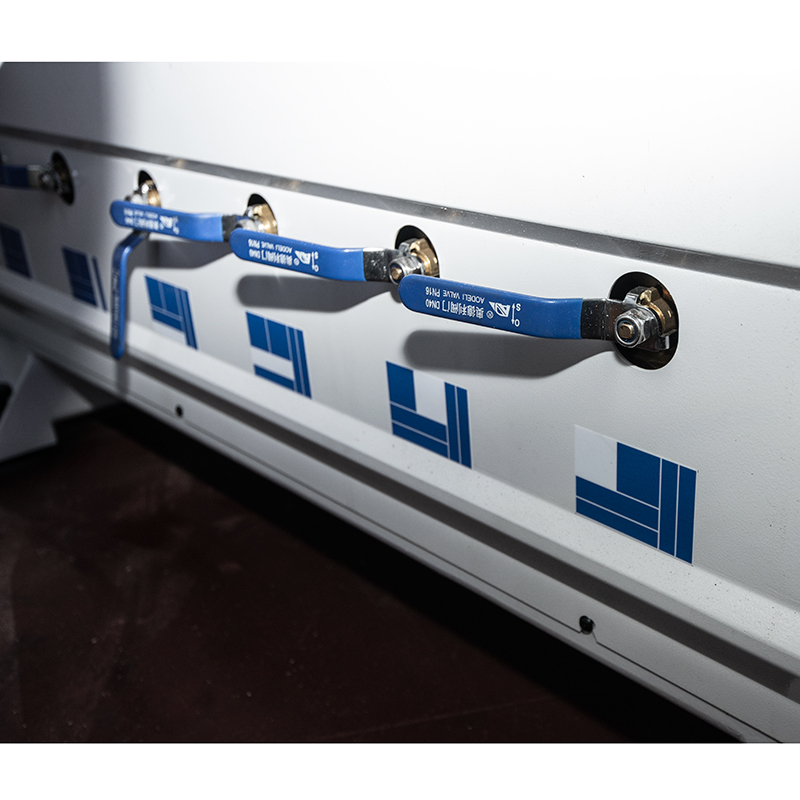
An efficient vacuum worktable is of primary importance for reliable processing of larger and smaller workpieces and energy saving.
The KDT KN-3710D machine has an industrial work table with an integrated vacuum chamber under the work table, which is part of the machine construction. A universal matrix work table is installed on the entire structure, which is pre-milled in its entirety, which increases the efficiency of the vacuum and ensures maximum adhesion of even smaller, more porous workpieces. This ensures the most efficient distribution of underpressure (vacuum) in combination with German BECKER pumps with a total capacity of 500 m3/h.
The construction concept and technology are common to high-end industrial CNC machines.
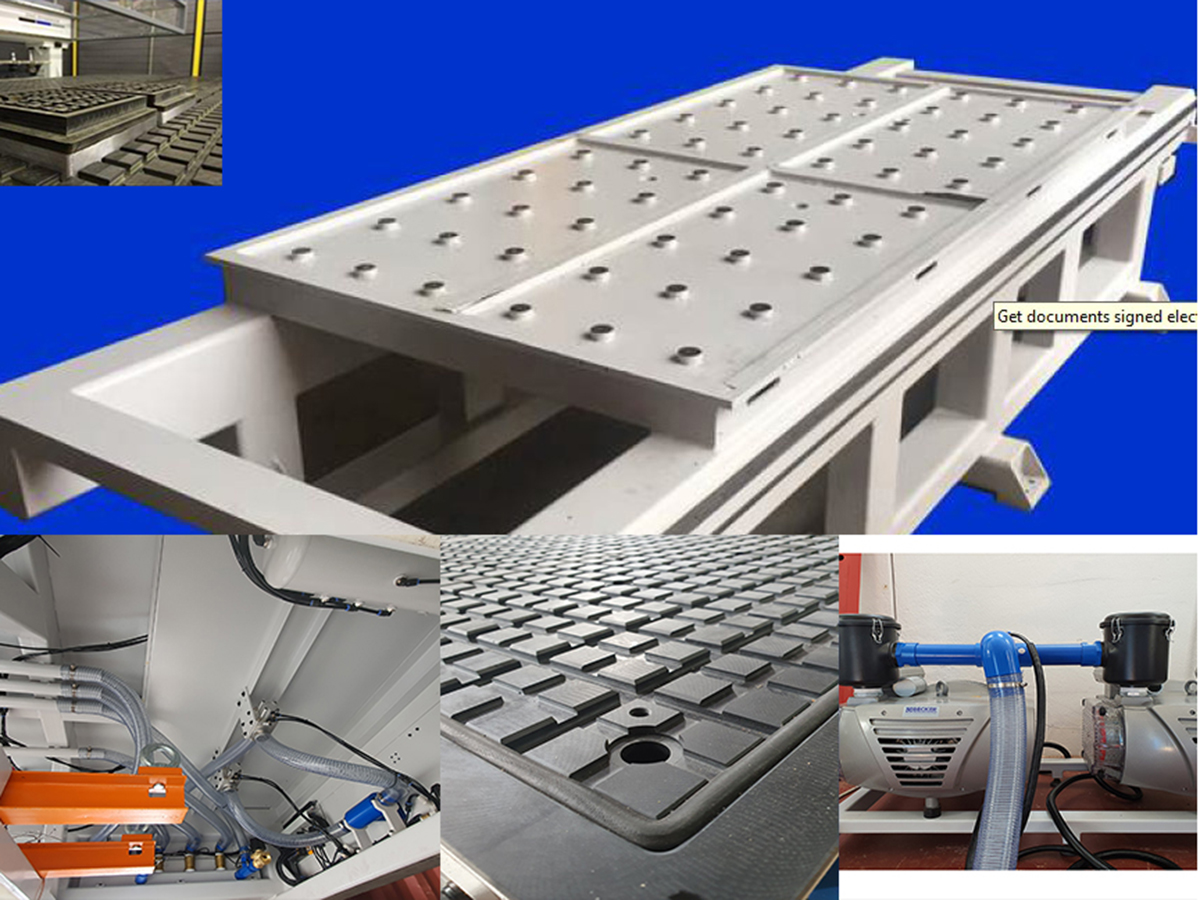
The machine is equipped with two BECKER VTLF.2.250 dry lamellar vacuum pumps with a power of 5.5 kW with a total flow of 500 m3/h. Possibility of retrofitting a third vacuum pump.
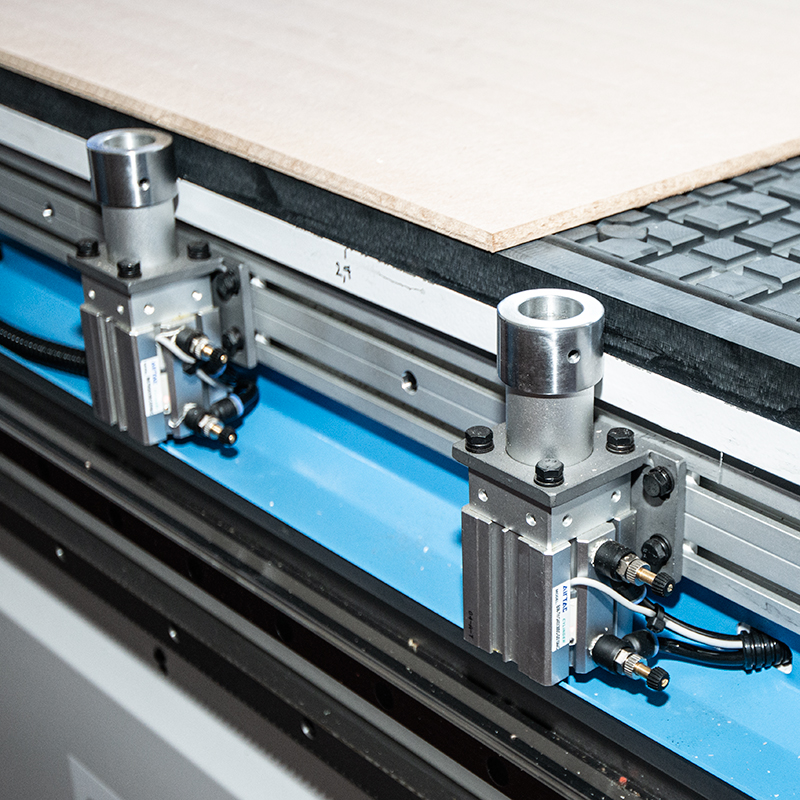
The machine has ten zero points made of solid aluminum. They are raised and lowered by pneumatic cylinders. They are integrated with a slat and safety sensors that prevent possible errors or injuries. The guide connected to the zero points has the function of more precise positioning of the workpieces and serves as a guide for the safe unloading of workpieces, especially of irregular shapes.
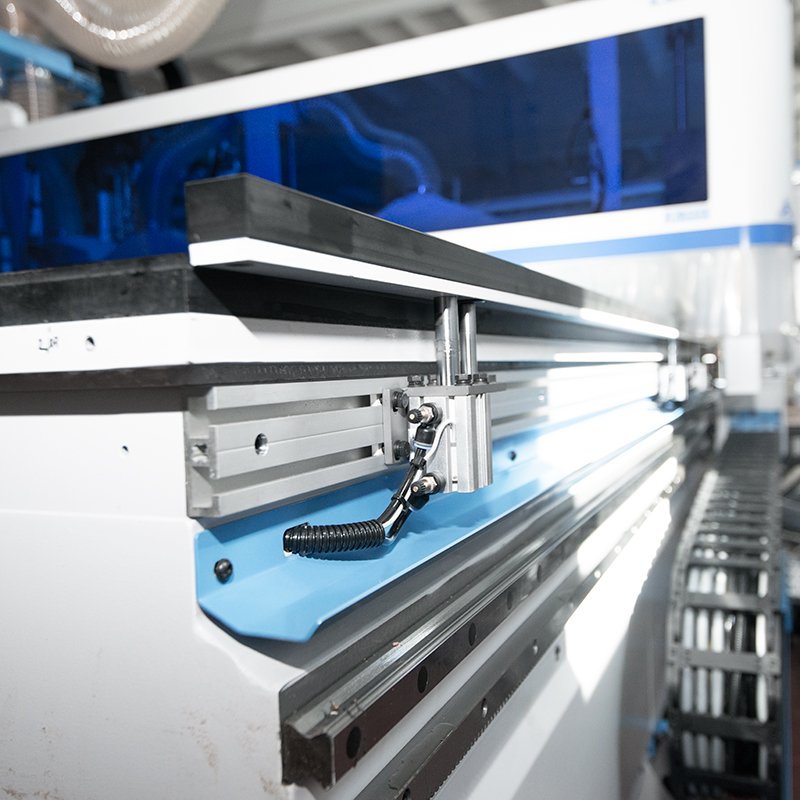
In the standard equipment of the machine there are alignment guides on the front side and on the left side. When the vacuum grippers pull the work plate onto the work table, the alignment guides align them to the position of the zero points.
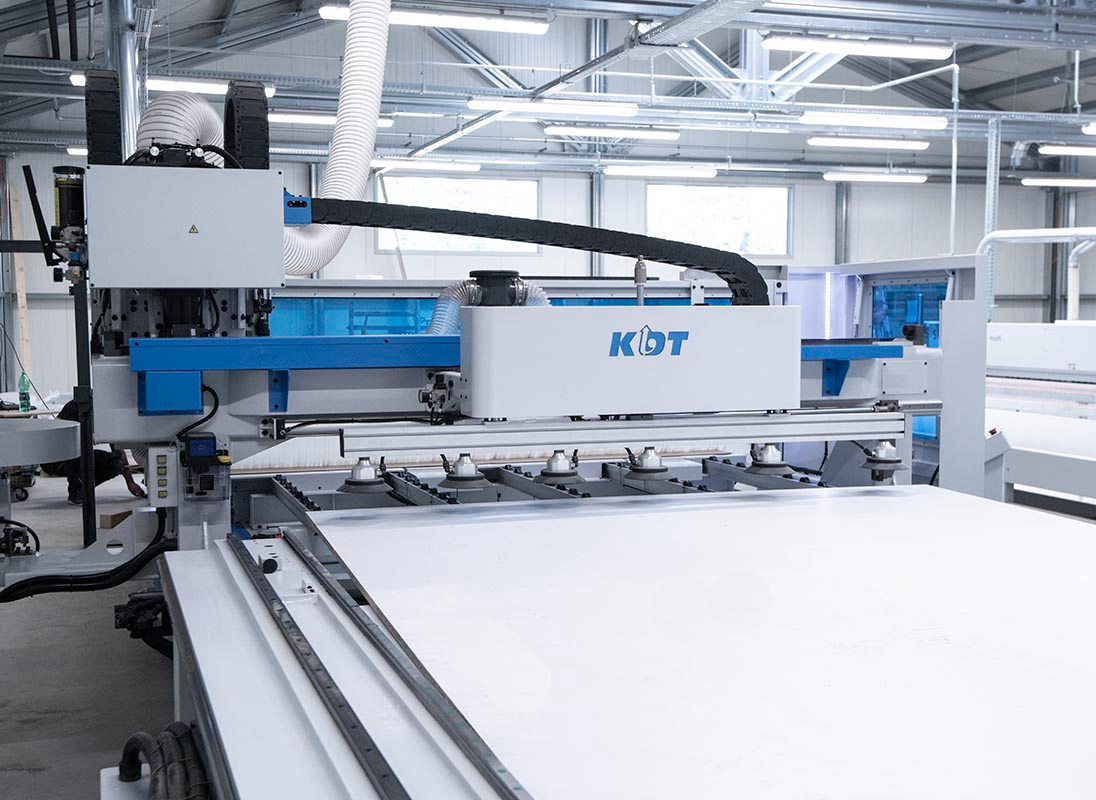
The vacuum loading device automatically pulls the workpieces from the lifting work table to the machine work table. It is assisted by side guides that position the workpiece on the work table.
The device is already included in the standard equipment of the machine, which means that we can upgrade the basic machine with an automatic lifting table at any time.
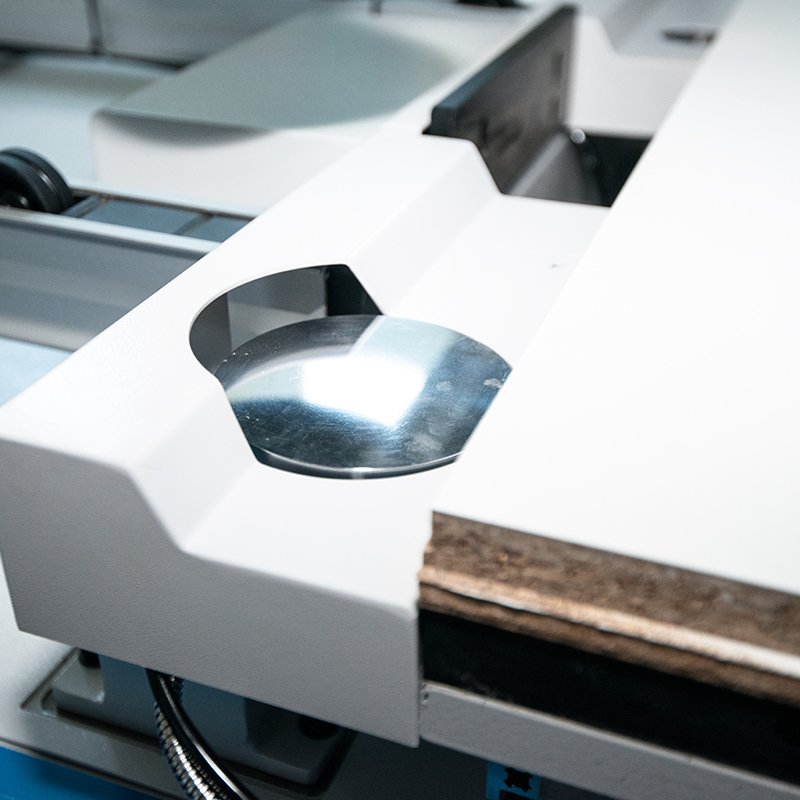
The tool length sensor is installed on the edge of the machine and enables the measurement of tools up to a diameter of 100 mm. The measurement of the entire tool in the magazine can be carried out automatically with the TPA software.
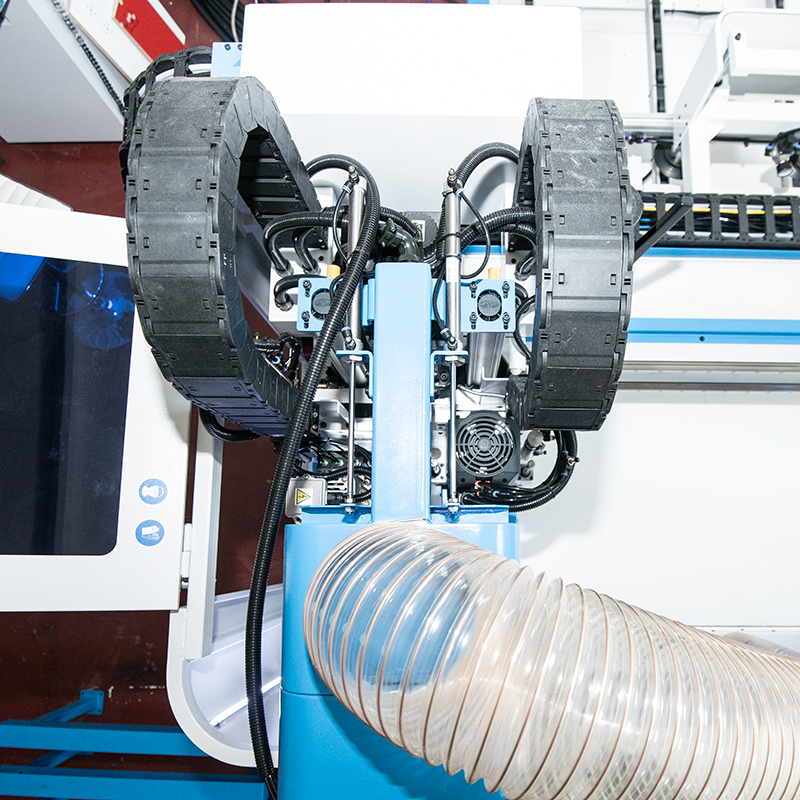
The reliability of the machine in industrial use depends on the quality of the cables in addition to the work units and guides. Continuous movement and direct sunlight can lead to cable wear, so KDT uses a top-quality power chain from the German manufacturer Helukabel, which ensures long-term reliable operation of the machine with minimal chances of breakdowns.
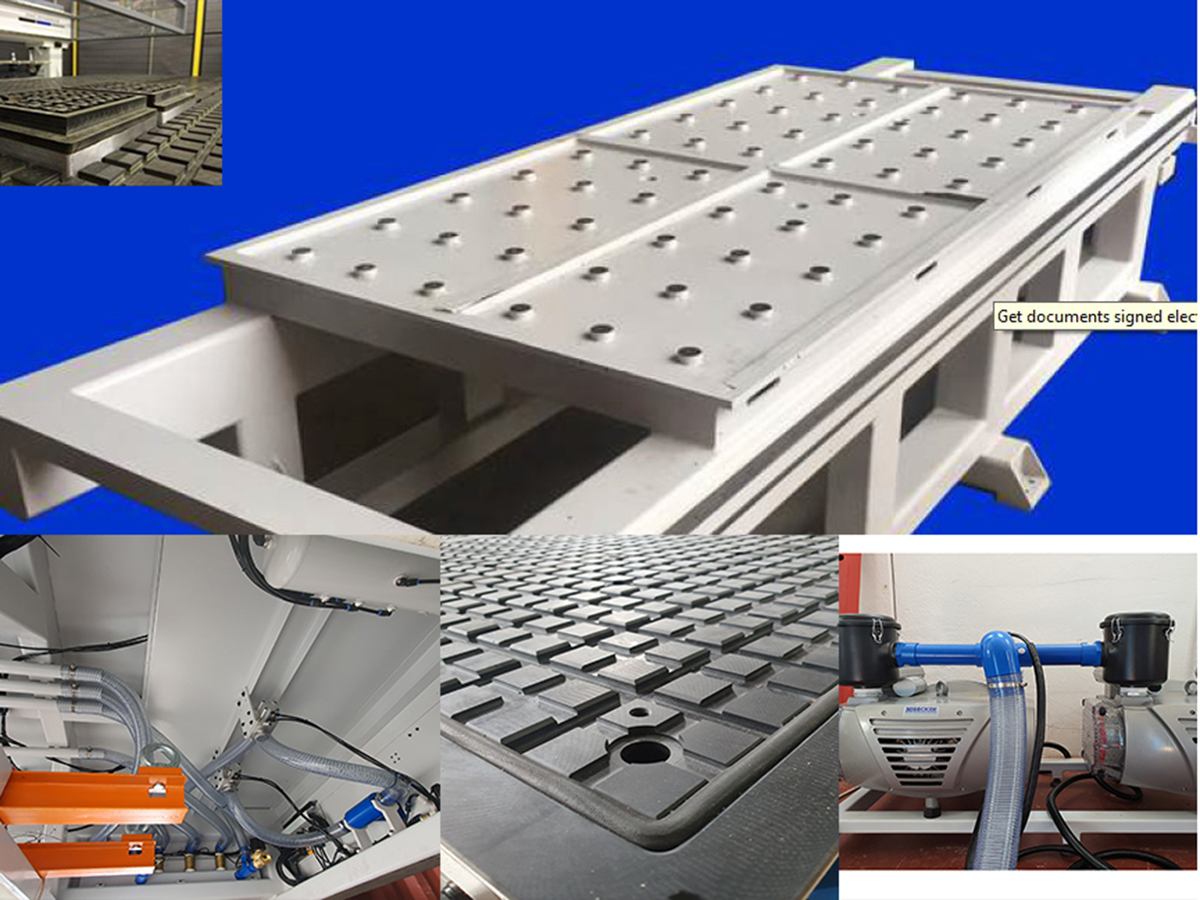
Robust construction is mostly reserved for more expensive industrial CNC machines with fast feeds. The purpose of this type of construction is to achieve zero or minimal vibrations that enable precision and high speeds and a long service life of the machine and components. The weight of the basic KDT KN-3710D machine is 4800 kg.
The KDT machine is made of a welded structure with double profiles of dimensions 260 × 160 mm, thickness 8 mm and transverse profiles 150 x 150 mm, steel thickness 8 mm. Everything is precisely welded, carefully and gradually heat-treated and cooled in order to prevent welding stress. The welded construction is only then completely processed on a five-axis CNC machine, which guarantees 100% precision, linearity and stability of the guides.
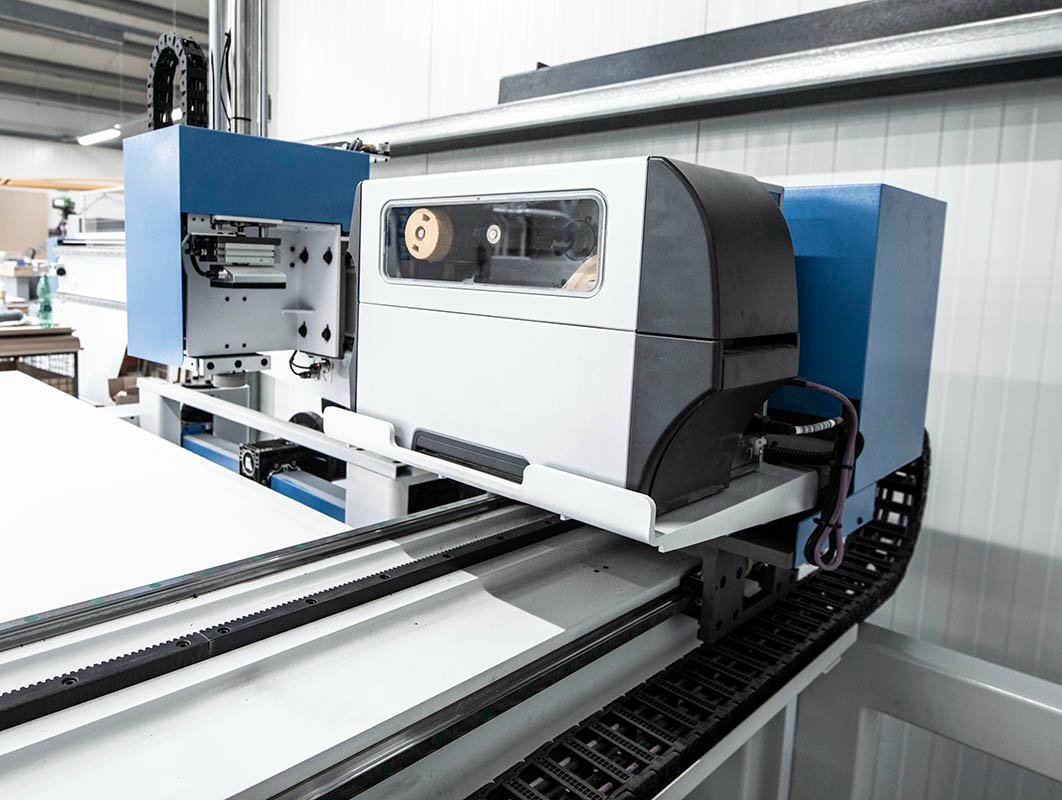
For the most demanding users, a version with automatic gluing of labels with black codes and data on individual workpieces is available with the ZEBRA ZT410 industrial printer and is significantly more affordable compared to competing providers.
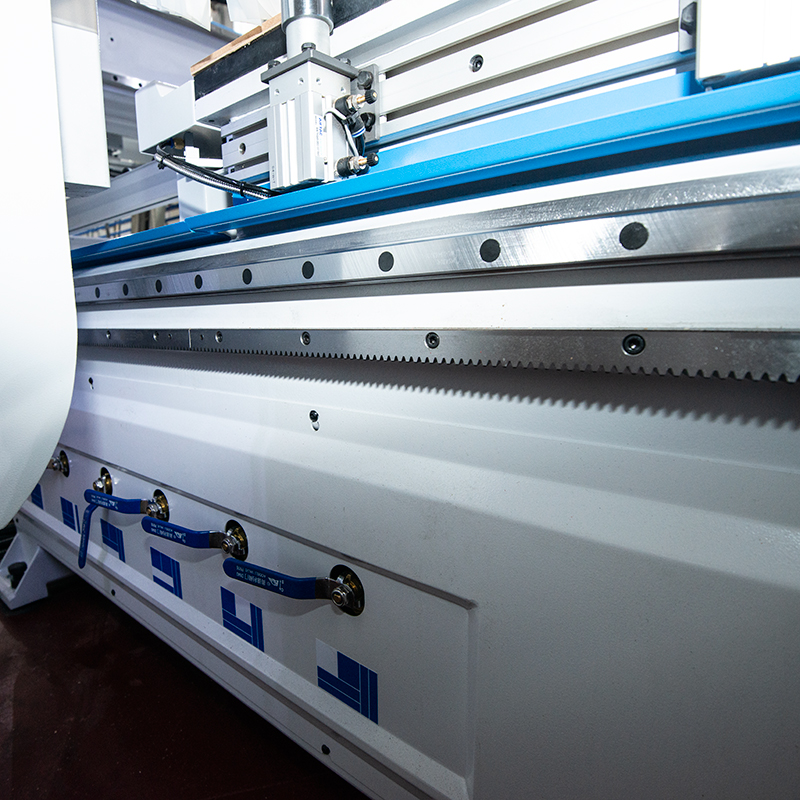
Guides along the X and Y axes have automatic guide lubrication, and along the Z axis with a manual pump.